Reducing Bioburden Risk with Workflow Best Practices
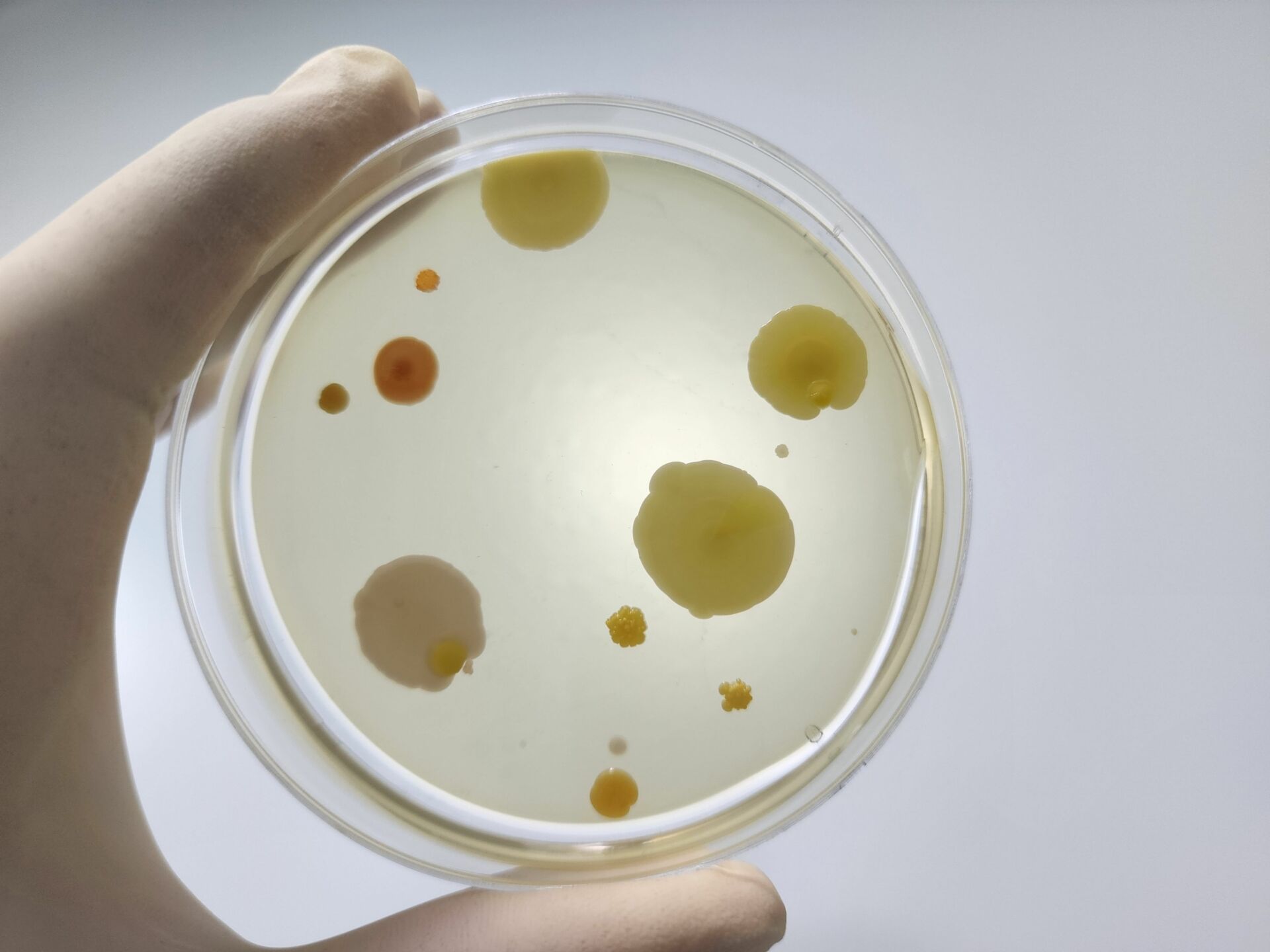
Recently, I read an article on Design for Contamination Control in sterile compounding areas. It was one of those publications that really got me thinking about best practices. A lot of the article was about where to place things like doors, lines of demarcation, and HEPA filters but the underlying theme was about how personnel and particulates move throughout compounding areas.
Many times, it’s the “not-so-great” things we do that can contribute unnecessarily to the bioburden in the clean room. We know that personnel and workflows are the greatest source of contamination. Following preparedness, hand hygiene, and garbing procedures is paramount, but we can look beyond the order we’re applying our garb, for example, and consider how the clean room design should inform our actions. We can also make recommendations for improvements when we encounter workflows that impede our ability to apply standards and best practices.
Here are some points this article made me think about:
- The “dirty” side of the anteroom should not be dirty.
In fact, this area should remain as clean as possible because it’s likely the location of the highest level of bioburden in the entire clean room suite. We should be limiting our time in this space – ideally reserving the anteroom for garbing and hand hygiene only.
- Be aware of where and how materials are disinfected.
A dedicated disinfection station, free of clutter and high particulate-generating sources, like cardboard, that is easily cleanable will allow for material transfer procedures to be carried out as aseptically as possible. It’s also important to ensure that contact times for the disinfecting agent used are met.
- Limit communication between garbed and ungarbed personnel.
Conversations should not occur in the anteroom. Speaking sheds high numbers of particles and can contribute unnecessary bioburden. We should never open a cleanroom suite door and keep it open while we speak to other personnel in the anteroom or cleanroom, especially if we’re ungarbed.
- Use an on-demand storage system.
When fewer items are stored in the cleanroom, cleaning can be done more efficiently. The article’s authors recommend storing no more than 1-7 days’ supply in the compounding area. Where supplies are stored is also important – when they’re stored closer to the floor, particulate can flow over them more easily and risk contamination.
The results of environmental monitoring in your compounding areas will help inform the need for workflow changes, especially if the cleanroom design does not meet all best practices.
What other workflow considerations can you think of that can reduce bioburden in compounding areas? Share your comments below.
About the Author: Teresa Hennessey is a pharmacy technician with 25 years of front-line and leadership experience in both community and hospital pharmacies. She is the Administrator for PTSA.