Reducing Medication Errors One Barcode at a Time
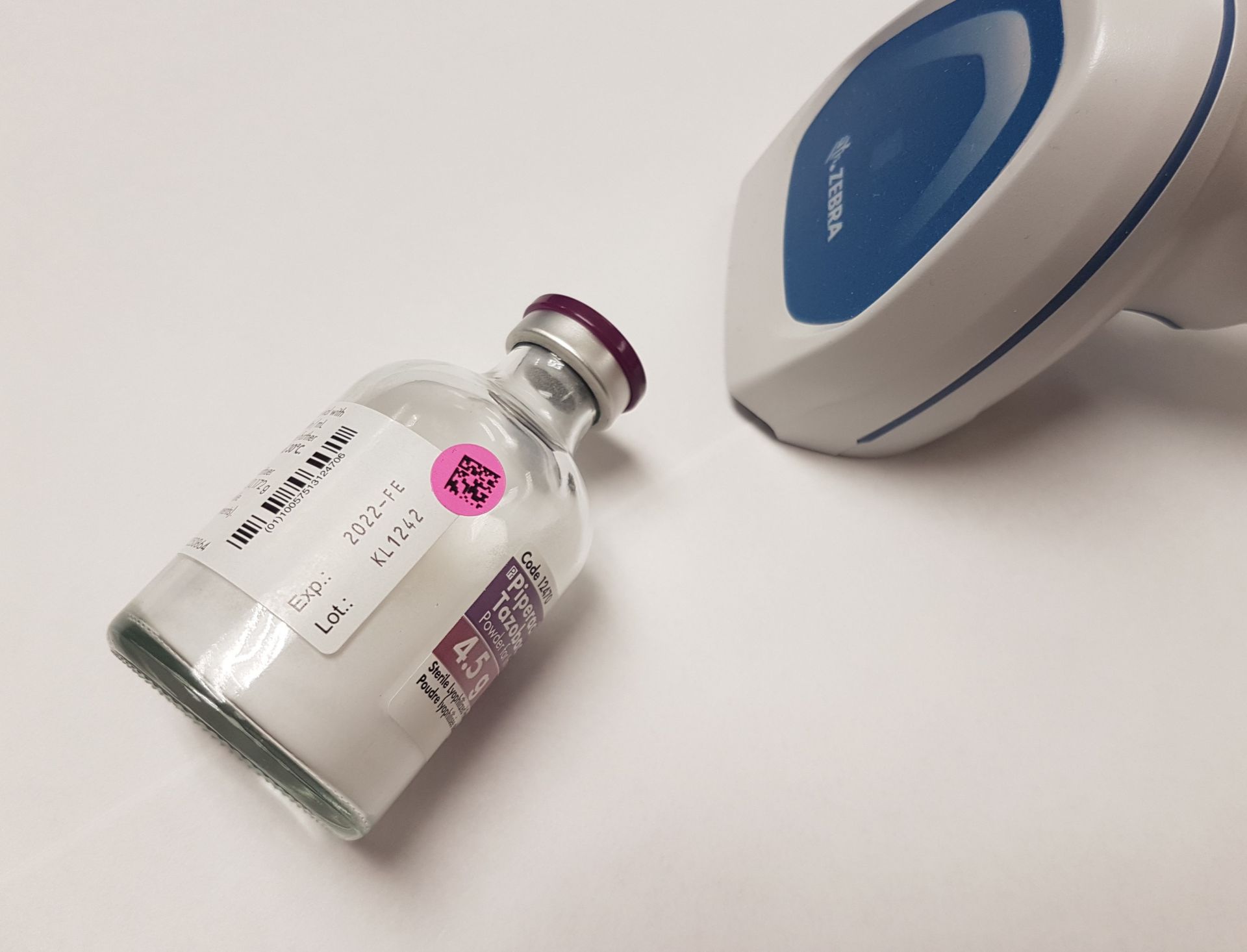
Where better to write my first blog post but on a work trip? So here I am! Hello everyone. My name is Samantha Bruun and I am a Pharmacy Technician currently working in three different pharmacy settings: Hospital, Retail and Corrections. My highlights and accomplishments throughout my career include receiving my Green Belt Certification which feeds my love for process improvement, completing multiple projects pertaining to creating efficiencies through all three pharmacy settings, and most currently taking on roles within Connect Care such as barcoding.
For those of you who do not know, Connect Care is a new way of using and sharing health information to improve patient care within Alberta Health Services (AHS). This will bring various changes to every zone, site, and department within the province. The one major change that I would like to discuss from a hospital pharmacy perspective is the process of barcoding and how our world as pharmacy technicians will expand even more than we have now.
Imagine being at the checkout counter at a store and the cashier is scanning your products. Now picture yourself in a hospital setting. That process is now the nurse scanning a medication to administer to a patient which is the final step to this new workflow. Where it begins though is within the pharmacy, which is the most crucial step in this new process. Every medication that is received from the vendor within the pharmacy department will need to be manually barcoded by the pharmacy staff before it is placed onto the shelves for distribution. To complete this task a pharmacy needs at least two pharmacy staff members, and as our final check roles have expanded as pharmacy technicians, we are essential for checking the initial and final product within the barcoding process.
What information is included in the barcode? The GTIN (Global Trade Item Number) for the medication which can be used to trace the drug’s DIN and package size, as well as variable data such as the lot and expiry. Every barcode is specific to that medication, and that information is within the new software system that the pharmacy will be implementing. So, when nursing scans a medication to administer a medication the system will identify an error if they have chosen the wrong medication, medication strength, or even if a medication has expired. Barcoding greatly assists nursing in following the 7 rights of administration, resulting in accurate and safe patient care.
You might be wondering why we cannot utilize the manufacturer’s barcode instead of manually labelling them. Unfortunately, not all manufacturer barcodes are compliant to Global Standards 1 (GS1) which means they do not include all the information required for the new software system to work appropriately. So that is why this task falls to pharmacy to ensure the correct barcode is affixed to the correct medication. On a positive note, there is an ever-expanding list of medications that are now exempted from being barcoded as the manufacturers are slowly progressing towards using fully GS1 compliant barcodes on their products which is also compliant within the new software system.
As you can imagine, this doesn’t only benefit patient care, but it also improves the pharmacy processes such as expiry pulling and drug recalls. This workload also follows the Closed Loop Medication Management process (CLMM) which is a fully electronic medication management process that means that from start to finish every step is accounted for. This process also increases the importance of ensuring the correct barcode is on the correct product which then gives the pharmacy staff that extra accountability of their work. For example, pharmacy staff must sign off on the new system when generating the barcodes, initial checks, and of course- the final check. This new process also prompts for a crucial overview of current workflows, workload, and prioritizing tasks which gives us as pharmacy technicians within a hospital setting the privilege to help bring these changes to light.
Well that is barcoding in a nutshell! The reason I wanted to broadcast this specific topic is to highlight a whole new world for hospital pharmacies. With all new processes there will be ups and downs, but with patient care being our main priority I am grateful that our organization decided to implement this process throughout Alberta. Coming into this, I understood that barcoding could help reduce medication errors, and that is the only reason I needed to assist with launching this new process. As to quote a provincial Barcoding Project Subject Matter Expert (SME), “This is an unprecedented time, and barcoding is an immense project that has not been implemented at this size and scale anywhere else in the world”. This is an opportunity to be involved in something that is groundbreaking, and as a pharmacy technician I am beyond excited to be involved in this change.